An introduction to Stratasys flexible photopolymers
Strength goes without saying, but countless modern applications require 3D printed parts that are also flexible, pliable and easy to manipulate. Stratasys’s range of flexible 3D printing photopolymers could be the answer – here’s an introduction to the best ones offered by Tri-Tech 3D.
What constitutes a flexible part?
Asking yourself what a component will be used for is the key to successful 3D printing. Sometimes, unbeatable strength is what’s required for a 3D printed part to excel. With other applications, the essential property might be stellar resistance to heat or chemicals. All of these criteria – and many more – can be satisfied by pairing the right printer and technology to the ideal material.
But what about parts that require unrivalled flexibility? From the sole of a new sports trainer to the simulation of soft tissue used by medical students to trial surgery, the demand from global industry for materials that bend and flex – without tearing or splitting – has never been greater.
As well as producing some of the sector’s most respected 3D printing hardware, Stratasys is also renowned for creating advanced materials that excel in scenarios where flexibility is paramount. Let’s take a closer look at why you might need them and some of the most popular examples.
Why would someone need a flexible 3D printed part?
Even products that appear to be tough and unyielding make frequent use of flexible parts. Consider a production line robot claw that is required to rapidly grab parts from a conveyor belt without scratching them, or the kind of jigs and fixtures that require a more delicate touch (both common uses of a flexible material like TPU 92A).
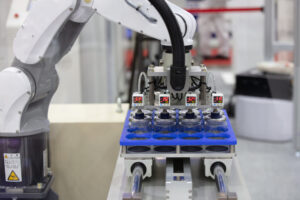
Of course, components such as these can be made using traditional moulding and casting – but the associated delay and expense simply can’t compete with additive manufacturing.
What applications could flexible materials be used for?
Here are just a few ideas of applications where flexible materials are used:
- Consumer – sports goods, food storage containers, rubber masks
- Medical – tissue simulation for pre-surgery training
- Tooling – jigs, fixtures, grips, gaskets, seals, handles and hoses
- Prototyping – rubber-like parts, surrounds and over-moulding
What factors should you consider when choosing a flexible material?
At Tri-Tech 3D, our team is ready to discuss your business-specific needs and pick out the material that will suit your application best. But if you’re assessing the merits of a given flexible material, there are five statistics to keep in mind.
Tensile strength
The maximum stress a material can withstand before breaking when it is pulled or stretched
Elongation at break
The measurement of a material’s ductility, showing how far it can be stretched, relative to its original dimensions, before breaking
Tensile tear resistance
The maximum mechanical tension that a material can stand before cracking
Shore hardness
The measure of how resistant a given material is to indentation
Polymerised density
The measure used to assess how uniform a material is
What flexible materials does Stratasys offer?
Stratasys’s flexible materials are almost as well-known as its 3D print hardware. Below are some of the most popular materials and their key properties.
Investigate TPU 92A for a tough thermoplastic polyurethane whose flexibility and stretch combines with great resistance to tearing and abrasion. Ideal for producing high-quality elastomeric parts, we’ve seen TPU 92A used for everything from cooking utensils to custom gaskets.
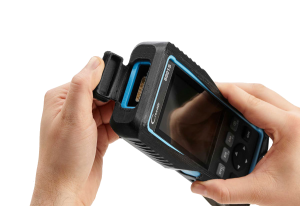
Consider Agilus30 for rapid prototyping and advanced design verification. This high-quality PolyJet photopolymer is an ideal substitute for rubber-based products, simulating the look, feel and uses of that traditional material and helping to create parts that can flex and bend repeatedly without tearing.
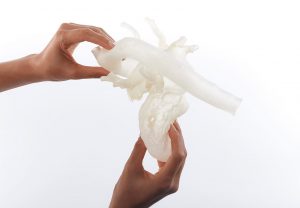
Alternatively, many of our clients are impressed by Elastico for design verification and prototyping. Both are rubber-like PolyJet photopolymers that excel in LED curing systems.
Of course, this is just a taste of the specialist materials – flexible or otherwise – available from Tri-Tech 3D. Contact the team, tell us a little more about your application and we’ll guide you to the flexible material that makes sense.
Get in touch with Tri-Tech 3D for guidance on flexible materials and more
Many of the UK’s most innovative companies have trusted Tri-Tech 3D to introduce 3D printing capabilities to their business. With a comprehensive selection of 3D printers from globally respected brands including Stratasys, we can also offer the materials, software, training and support to embed AM capabilities in your firm and ensure you hit the ground running.
Just drop a line to Tri-Tech 3D and we’ll be glad to tell you more about our 3D printing solutions. You can reach us on 01782 814551 or info@tritech3d.co.uk