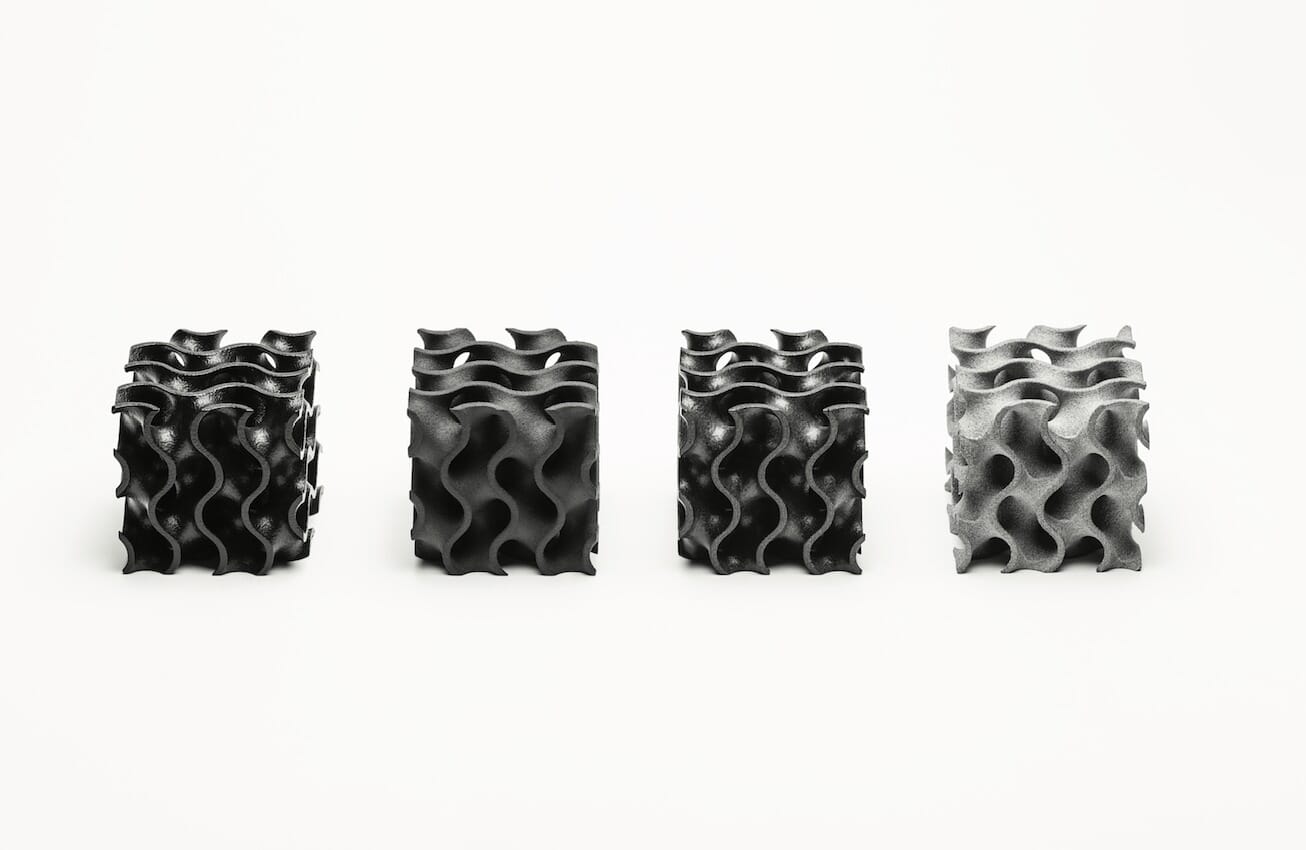
STRATASYS SAF™ 3D PRINTERS
Boost your manufacturing capability with powder bed fusion 3D printing
What is Selective Absorption Fusion (SAF)?
Selective Absorption Fusion (SAF) is a groundbreaking technology that has transformed parts production worldwide. It originated from the well-known AM technique of powder bed fusion. At the heart of 3D printers like the Stratasys H350, the SAF process sees piezo-electric printheads jetting high absorption fluid (HAF) onto a powder bed, with the fluid then fusing the powdered polymer particles in layers to create parts.
Choosing a professional SAF 3D printer allows you to access production capabilities that traditional methods like injection moulding cannot provide. This choice also helps you avoid challenges such as high tool-up costs, build capacity limits, and supply chain delays. This also helps in avoiding challenges like high tool-up costs, build capacity limits, and supply chain delays. SAF is one of the fastest-moving technologies in the additive manufacturing sector, and at Tri-Tech 3D, we’re proud to offer the hardware and expertise to let you keep up.
Tri-Tech 3D’s experts are always on-hand to advise on the best SAF 3D printers for your needs, including the market-leading Stratasys H350. For consistent, repeatable, high-quality results when prototyping or rolling out production, this best-in-class model is an excellent place to start.
Below, you’ll find SAF benefits at a glance, alongside answers to some of our clients’ most common questions, case studies and all the models in our range.
SAF 3D printing benefits
-
Agile & flexibleWhile it’s best-known for volume-quantity production, SAF can produce intricate and complex parts at pace, making it equally suited to rapid prototyping and tooling.
-
Consistent qualityWith more precise thermal control over the build process relative to other powder bed technologies, SAF eliminates quality issues and warping.
-
Repeatability & reduced costThe ultra-consistent part properties associated with SAF mean reliable print runs, higher yields and lower cost-per part.
-
Fewer consumablesThe piezo-electric print heads used in SAF are non-consumable, while the need for just one fusing fluid cuts operational costs and saves on future maintenance.
-
Reduced wasteWith any powder overflow recirculated, SAF eliminates waste and reduces your long-term spend on materials.
-
Production at scaleThe generous build volume of SAF 3D printers like the Stratasys H350 allow high-volume production and simultaneous prototyping of multiple design iterations.
CASE STUDY
STAFFORDSHIRE UNIVERSITY - Objet 30 Pro printer
There are many companies selling 3D Printing Technology but not all are equal! We chose Tri-Tech3D as our supplier of choice due to their flexibility in matching our requirements, their technical knowledge and their support arrangements. We are confident we made the right choice as we have now doubled our RP capacity and added a new technology in the form of an Objet 30 Pro printer which is delivering exceptional quality models.
-
What are the different types of powder manufacturing process?
The Stratasys H350 – powered by proprietary SAF technology – is just one example of powder bed fusion. In fact, powder bed fusion is a broad term that covers several different AM technologies. The five most common are direct metal laser sintering (DMLS), selective laser melting (SLM), electron beam melting (EBM), selective laser sintering (SLS) and multi-jet fusion (MJF). Each technology has its own associated hardware, materials and specialisms, so take advice from the Tri-Tech 3D team before making a decision.
-
How does powder bed fusion work?
Let’s take the example of the SAF technology within the H350, which is specific to this line of Stratasys 3D printers. Specialised print heads spray special fluid onto specific areas to create each part's layers. Infrared energy then melts and fuses the layers together." Particles of polymer powder are fused into cohesive layers for part creation, while proprietary Big Wave powder management technology ensures even powder distribution. The result is exceptional quality and precision, repeatable at scale.
-
What industries use powder bed fusion?
Thanks to its quality and consistency – alongside the ability to create complex one-off geometries – powder bed fusion is a mainstay across the gamut of global industry. Products created using AM technology are used in different industries. For example, Bugatti utilised it to manufacture titanium brake callipers in the automotive sector. In the medical field, surgeons employed powder bed fusion to produce a personalised replacement jaw bone.
-
What materials are used in powder bed fusion?
Like all AM technologies, powder bed fusion offers an almost infinite choice of compatible materials. Many of our clients have achieved successful results with materials like PA11 engineering-grade polymer and tough PA12 polyamide. But depending on the specific technology, 3D printer and application, you might also use traditional metals including aluminium and stainless steel, or superalloys like inconel. At Tri-Tech 3D, we’re always ready to listen to your production goals and advise you on the optimal materials.
-
Is powder bed fusion slow?
In general terms, powder bed fusion is considered one of the slower AM technologies (due to the associated processes of powder preheating, vacuum generation and cool off). By contrast, the SAF-powered Stratasys H350 is recognised as one of the fastest models on the market, not only delivering components quickly but offering a generous build size (315x208x293mm) that lets you manage multiple part-creation and ambitious builds that smaller hardware cannot accommodate.
-
What is the strongest additive manufacturing process?
While every additive manufacturing discipline has its pros and cons – from accuracy to repeatability – strength is a category where powder bed fusion is acknowledged as a sector leader. This technology allows components to handle stress in demanding industries like aerospace and motorsport. This is due to their intricate designs and strong materials.
Most popular SAF 3D Printers
-
Production Parts
The H350 printer with SAF technology offers a generous build volume that accommodates high-volume production.
-
End-of-Arm Tooling
Reduce the weight and cost of robotic end-of-arm tools by 3D printing them with SAF technology.
-
Automotive & Transportation
Improves efficiency with lightweight, durable parts; reduces emissions and inventory costs through on-demand manufacturing.
-
Industrial and Packaging Machinery
Enhances machinery reliability with precise, durable components; streamlines production with rapid prototyping and manufacturing.
-
Consumer and Sporting Goods
Offers customisation and innovation in products; enables rapid market introduction of high-quality, tailored sport and consumer items.
-
Orth Drones
Enables lightweight, high-strength component manufacturing; optimises designs for fuel efficiency and paotics facilitates production of custom-fit, anatomically precise orthotic devices; improves comfort, support, and accessibility.
-
General Manufacturing
The fine details and repeatability of SAF make it an optimal choice for small machinery parts.
New to 3D
Printing or looking
for some support?
- Call: 01782 814551
- Email: info@tritech3d.co.uk