Optimising human machine interface prototypes with the Stratasys J35 Pro
APEM Components specialises in the design and manufacture of HMI parts, including panel switches, joysticks, LED indicators and industrial controls such as emergency stop switches. The company wanted to produce high-quality prototypes with elaborate designs in multiple materials, which it could showcase to customers at trade shows and site visits.
Tri-Tech 3D supplied APEM Components with a Stratasys PolyJet multi-material additive manufacturing (AM) system, which would improve the quality of human machine interface (HMI) prototypes.
The challenge
When it started its 3D printing journey a few years previously, APEM invested in an FDM system. While this system offered APEM a sophisticated in-house printing capability, the printed parts often contained visible lines and the company still relied on bureaus to create the occasional gasket or gaiter, which extended lead times and increased overall costs.
The solution
Originally, APEM wanted to print using multi jet fusion (MJF), but this technology would require extensive set-up and post-processing — extending labour and other costs significantly. Instead, Tri-Tech 3D suggested the Stratasys J35 Pro because it is easy to use, intuitive and has minimal maintenance requirements.
Users can create models with rubber-like characteristics, as well as high-impact, rigid, translucent and biocompatible components. Manufacturers can use up to three filaments during one build, which reduces overall production time by avoiding the need for multiple printing shifts.
See below a part from APEM. This 3D Printed alignment jig allows APEM to drill holes into a moulding for pushbuttons, this is for an end customer prototype. If APEM then go in to production they would create a tooling mod to mould with these new pushbutton positions.
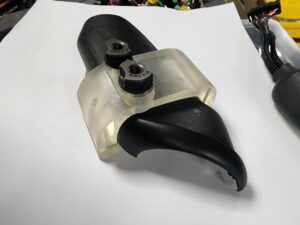
The J35 Pro offers a high print resolution, and users can mix and match resins. Currently, APEM is printing with Vero DraftGrey, Vero UltraClear, Vero UltraBlack and Vero UltraWhite. The ability to print transparent parts means customers can now see how internal components work together.
Results
APEM has seen an improvement in customer engagement because of the new AM system. It is now creating high quality models that resemble the finished product more closely, which is helping the company close more deals with customers.
Howard Spink, Senior Design Engineer at APEM Components commented:
By bringing the J35 Pro on board, we can now print a wider range of prototypes from the comfort of our facility, and we are less reliant on bureaus. Importantly, we can create high-quality parts with shorter design cycles than before.
With the J35 Pro, APEM can print prototypes in high resolutions, which has facilitated the testing of intricate moving parts. With the previous machine, the company was unable to do this, so the new equipment has shortened prototype development significantly.
To discover how Tri-Tech 3D’s PolyJet equipment and support can help your business, get in touch.