Top tips for saving energy when using your FDM 3D Printer
Energy prices never get lower, and with global climate change, those prices will likely only increase. At the moment in the UK – energy prices are higher than ever so we wanted to give you some tips on how to keep the costs down when running your FDM 3D printer.
Although FDM 3D printing technology offers cost efficiencies compared with traditional manufacturing, like any industrial equipment, it consumes energy, which costs money. However, there are ways to reduce your printer’s energy cost footprint, and they’re relatively easy to implement. This article will show you how to lower your FDM printers’ energy consumption and, as a result, your energy bill.
Practice Good DFAM (Design for Additive Manufacturing) ✏️
Before we even consider the printer, there are a few things you can do to reduce your part’s weight and build time. There is a direct link between these factors and energy consumption because printers consume more energy during active printing than when idle. As such, designing for shorter build times will often yield the greatest savings.
It’s very tempting to design parts big and blocky, just like you’re used to for CNC manufacturing. But for additive manufacturing, you can take a very different approach. Take a look at the ULTEM™ 1010 resin composite form tools below.
The shell-style tool uses less material, prints in less time, and uses less energy compared to the sparse-style tool. By taking advantage of 3D printing’s design freedom and considering different design options, you can positively impact your results, including reducing the energy required to produce them.
Additionally, support material can be eliminated or significantly reduced through clever design. The parts below are nearly identical except for how specific features are designed.
Adding self-supporting angles where possible means there’s no need for soluble support because the model material is “self supporting” – a key feature of FDM technology.
If you or your team want more information on DFAM, please get in touch or take a look at our DFAM training course.
Replace Support with Model Material 💪
For faster prints on Fortus systems such as the Fortus 450mc and the F900, consider using print settings that replace support material with model material. This reduces the number of swaps required between model and support tips, decreasing print time. With F123 Series™ printers, this effect is negligible. Review your model when using this setting, as it may increase the difficulty of removing support material for certain geometries.
In GrabCAD Print™, this option is found under Support Settings.
With Insight™ software, this option is found under Support -> Support Setup -> Support Parameters.
Shut it, don’t slam it! 🚪
One of the reasons Stratasys FDM technology is best-in-class is the fully heated build chamber. Having such tight control over the build envelope improves accuracy and part strength. Leaving the printer door open for prolonged periods wastes heat to the atmosphere. Slamming the door can also introduce an influx of cold air, wasting more heat. So just like your parents always said, shut the door, don’t slam it.
Enable Automatic Energy Saving Mode 🔋
You may not be aware your printer already has an automatic energy-saving mode built in. Once enabled, the system will automatically disable the heaters after two hours of idle status when printing has finished. This lets parts cool down slowly and save energy if you’re not planning to restart the printer immediately.
For F123 Series printers, this setting is under Settings, Standby Mode in the printer’s user interface.
For Fortus printers, system defaults can be changed from the System Default menu (Fortus 900mc and F900), and the Settings Page (Fortus 450mc), located through the respective printers’ touchscreen.
Don’t Waste Compressed Air 💨
Fortus systems use compressed air to generate the vacuum that keeps your build sheets held firmly to the build bed. However, once printing is complete and the system is idle, turn the bed vacuum off by selecting the vacuum control icon on the machine’s touch screen to save compressed air consumption.
Support Removal Tanks ✋
For the fastest results, support removal tanks need to be heated. But the quickest way to remove supports is not to print them in the first place, as we explained earlier.
When you do have to use support, it is often possible to manually remove it from your part. The best way to do this is to use heat-resistant gloves and pliers to pull the support away from your part while it is still warm from the printer. Don’t worry if you can’t get it all; you can still use the tank, but by removing big bulky areas of support, you’ll reduce your tank times.
Finally, depending on your manufacturing schedule, you could also consider turning off the heat on your support removal tanks or reducing the temperature at night or over the weekend. Support material will still dissolve at lower temperatures, just more slowly.
Nesting and Scheduling High-Temperature Builds Efficiently 🌡
If operating a system that regularly swaps between high and low-temperature materials, consider grouping parts together to avoid unnecessary material changes and temperature stabilisation periods.
Advanced Tips
System Location and Heating vs. Cooling 📍
Like a lot of industrial equipment, Fortus printers need to exhaust waste heat into the atmosphere. Careful consideration of how you locate your system could save you energy in more ways than one.
The following bullets outline ways to do this.
- Is your facility in need of heat?
Co-locating equipment in areas that need heating repurposes this waste heat from your system. Consider which methods of ventilation would enable this. For example, if you need to duct large amounts of exhaust out of the building, can this waste heat be recaptured by a heat pump or heat recovery unit?
- Is your facility in need of cooling?
Clearly, it’s not ideal to heat up an area that you wish to keep cool. However, if you’re unable to relocate your systems to a more efficient location, many customers have had success by strategically placing extraction ducting or hoods to capture the waste heat and remove it from the building before it can spread to other areas.
We have also seen basic partition walls used to great effect to subdivide manufacturing spaces to keep hot machines together and away from machines that prefer to run cooler.
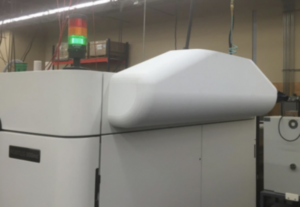
exhaust gases towards external ducting.
You should take care to match any external air extraction flow rates with the flow rate of the built-in ventilation system on the printer. Over- or under-extraction could alter the behaviour and print quality of the system. To help prevent this, vents can be added to the coupler which sits between the machine and external ducting to provide a separation point in the system. Below shows an example of this type of coupler-made with FDM additive manufacturing.
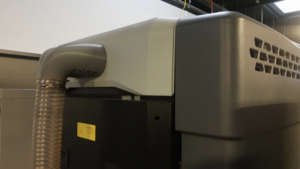
Hopefully this article has given you several strategies to decrease energy consumption when printing with FDM technology. Stratasys recommends reviewing your system settings and build parameters to see how you can improve energy efficiency and increase or maintain productivity. For more information, contact our team.