Ceramaret to install Carmel 1400C solution in its Swiss facility this year
XJet has announced that Ceramaret, a renowned technical ceramic manufacturer based in Switzerland, has acquired an XJet Carmel 1400C Additive Manufacturing system. Ceramaret’s investment followed an intensive benchmarking process driven by the verdict that XJet’s NanoParticle Jetting process could produce parts the team had previously deemed not possible.
About Ceramaret
Ceramaret, based in Bôle (CH) and Meissen (DE) designs and manufactures components from ultra-hard materials, such as advanced ceramics (zirconia, alumina, silicon nitrides and carbides) and synthetic sapphire and ruby. Ceramaret enables its customers and partners to benefit from its decades of experience in the shaping and machining of advanced ceramics and hard materials.
Through its activities, it occupies a leading position in the analytical, fluid-handling markets, as well as in watchmaking and selected medical applications. Ceramaret became part of the Kowema AG group of companies in 2014.
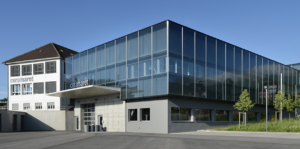
Senad Hasanovic, Ceramaret VP of Innovation commented:
XJet technology will provide us with new capabilities, new geometries we can offer our customers, whilst also delivering exceptional time-to-market. Taking 72 hours from a new file to a finished part, it’s an extremely fast process. However, it was the quality and global cost-per-part that really impressed me, demonstrating that this was an industrially competitive solution.
Masters of the whole ceramic production process, from design and prototyping to the mass production of high-precision advanced ceramic parts, the Ceramaret team regularly benchmarks technologies from across the industry.
Ceramaret has collaborated with XJet to test an impressive 30 distinct products with around 300-400 manufactured parts. Hasanovic and his team also visited XJet’s state-of-the-art Additive Manufacturing Center in Rehovot, Israel, witnessing the entire production process firsthand.
Hasanovic continued:
We scrutinised each of the test parts, polishing them and checking their structural integrity, their porosity, functionality and more. These investigations convinced us that the parts would meet the needs of our customers and add value to the manufacturing services we offer.
XJet uses nano particles to deliver extremely fine detail and accuracy. Meanwhile, the production of internal cavities or channels – typically a labour-intensive post-processing challenge or sometimes an unattainable feat with other technologies – is rendered straightforward with XJet’s proprietary soluble support material, which simply dissolves away.
Hasanovic describes XJet post-processing as “a repeatable, stable, industrial-grade process that we feel already familiar with.”